旋转执行器的核心构成与工作原理
旋转执行器的本质是将某种能量转化为旋转机械能的装置,其结构通常围绕 “动力源 - 传动机构 - 控制单元” 三大核心模块展开。
动力源是执行器的 “心脏”,常见类型包括电动、气动和液压三种。电动执行器以电机为核心,通过直流或交流供电实现能量转换,具有控制精度高、响应速度快的特点;气动执行器利用压缩空气驱动,适合高温、防爆等特殊环境;液压执行器则依靠液压油的压力传递动力,能输出较大扭矩,常用于重型机械场景。
传动机构如同执行器的 “关节”,负责将动力源的运动转化为精准的旋转动作。齿轮组、蜗轮蜗杆、谐波减速器等是常用的传动部件,它们通过减速增扭、调整旋转方向等功能,确保执行器输出符合工况需求的转速与扭矩。例如,谐波减速器凭借柔性齿轮的弹性变形实现传动,能在紧凑结构中实现高精度减速,广泛应用于机器人关节。
控制单元则是执行器的 “大脑”,由传感器、控制器和驱动电路组成。传感器实时监测旋转角度、速度等参数,控制器根据预设指令与反馈信号进行运算,驱动电路则调节动力源的输出,形成闭环控制,确保旋转动作的准确性。
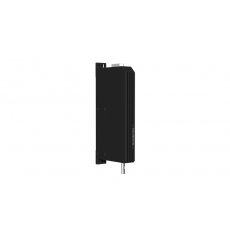
技术特性:精准与可靠的双重追求
旋转执行器的技术优势集中体现在三个维度:精度、扭矩与适应性。
角度控制精度是其核心指标,高端产品可实现 0.1 度以内的定位误差,这得益于精密传动部件与伺服控制技术的结合。在电子芯片封装中,执行器需带动焊头完成微米*旋转,误差过大会直接导致产品报废。
扭矩输出范围覆盖从毫牛?米到千牛?米,小扭矩执行器可用于光学镜头调焦,大扭矩产品则能驱动船舶舵机。通过模块化设计,同*基座可搭配不同动力源与传动组件,满足多样化扭矩需求。
环境适应性是执行器的 “生存能力”。工业*产品通常具备防尘、防水(IP65/IP67 防护等*)、耐高低温(-40℃至 120℃)等特性,部分特殊型号还能抵抗振动、冲击与电磁干扰,在航天卫星的姿态调整、深海探测设备等*端环境中稳定运行。
应用场景:从工业到民生的广泛渗透
旋转执行器的身影已遍布现代社会的诸多*域。在工业自动化生产线中,它驱动传送带转向、控制机械臂末端旋转,实现物料的精准搬运与装配;在智能家电*域,扫地机器人的万向轮转向、空调导风板的角度调节,都依赖小型执行器的配合。
机器人技术是执行器的重要舞台。协作机器人的肩部、肘部关节通过多个执行器协同动作,可完成类似人类手臂的灵活旋转;手术机器人中,执行器带动手术器械实现亚毫米*旋转,为微创外科手术提供稳定支撑。
在新能源*域,光伏跟踪系统通过旋转执行器调整太阳能板角度,使面板始终正对太阳,提升发电效率;风力发电机的偏航系统则依靠大扭矩执行器驱动机舱旋转,确保叶片对准风向。
发展趋势:智能化与小型化并行
随着工业 4.0 与物联网技术的推进,旋转执行器正朝着 “更智能、更小巧、更**” 的方向演进。智能化方面,执行器将集成边缘计算能力,通过 5G 或工业以太网实现设备间的数据交互,自主完成故障诊断与参数优化。
小型化与轻量化是另*重要趋势。新材料(如碳纤维复合材料)的应用降低了部件重量,微机电系统(MEMS)技术推动毫米*执行器的研发,为微创手术机器人、微型无人机等设备提供动力支持。
同时,绿色节能成为技术创新的焦点。无刷电机的普及降低了能耗,能量回收技术可将制动过程中产生的电能反馈至电网,在碳中和目标下,环保型执行器的市场需求正快速增长。
从工厂的自动化生产线到家庭的智能设备,旋转执行器以其 “转动” 的力量,支撑着无数精密操作的实现。随着技术的不断突破,这个看似普通的机械部件,还将在更多未知*域绽放光彩,推动人类对运动控制的探索迈向新高度。